Understanding Laser Beam Welding: The Future of High-Precision Metal Joining
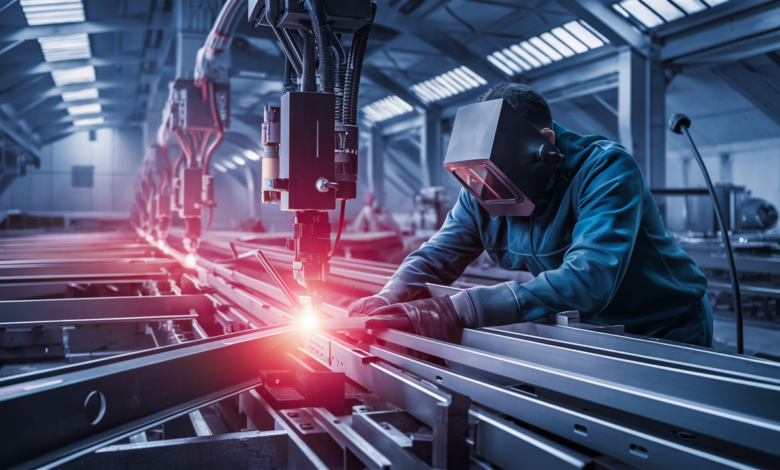
Laser beam welding is a modern welding technique that uses a powerful laser to join metal parts together. This method allows for extremely precise and fast welds, making it ideal for industries that need high-quality and efficient results. Whether you’re working with thin materials or thick metal sheets, laser beam welding can offer a strong, clean weld every time.
One of the best things about laser beam welding is that it doesn’t require extra filler material or a lot of post-processing, which saves time and money. The laser’s concentrated heat melts the material precisely where it’s needed, ensuring strong and reliable results. In this post, we’ll dive into how laser beam welding works, its advantages, and why it’s becoming the go-to choice for many industries.
What is Laser Beam Welding? A Simple Explanation for Beginners
Laser beam welding is a process where a strong laser beam is used to melt metal parts together. It’s a fast and precise way to weld materials, making it popular in industries that need high-quality and detailed work. The laser beam is focused on a small area, where the heat melts the material, and then it cools down and hardens to form a strong bond.
This method is different from traditional welding techniques like MIG or TIG welding. While MIG and TIG welding often use wires and electrodes to join materials, laser welding uses light energy. The laser beam creates enough heat to melt the metal parts, which then fuse together as they cool. This process is much faster and doesn’t need extra materials, making it a more cost-effective solution in many situations.
How Laser Beam Welding Works: A Step-by-Step Guide
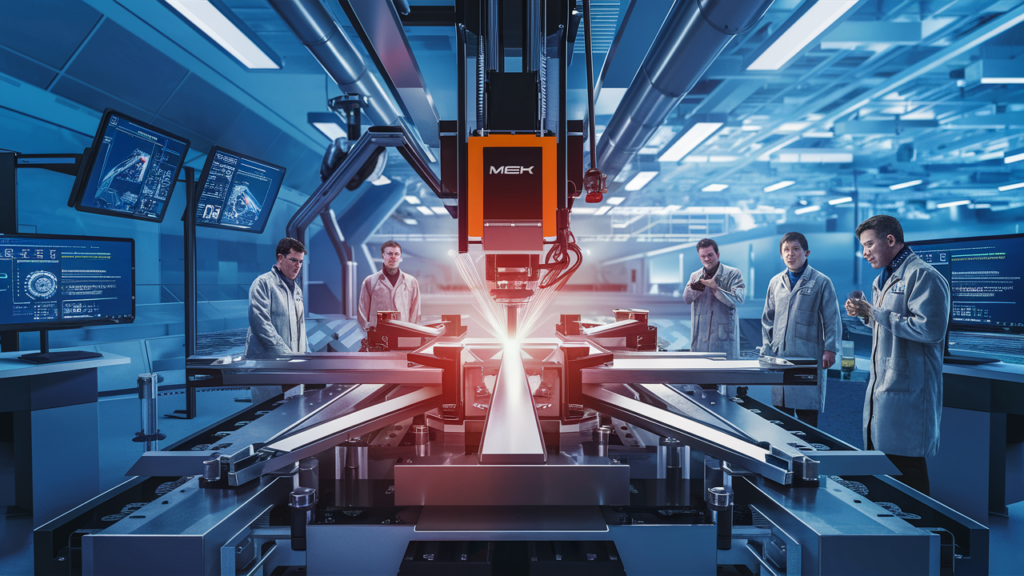
Laser beam welding involves several steps that ensure a clean and strong weld. First, a laser is created and focused into a beam using special lenses or mirrors. This beam is aimed at the material to be welded, and the intense heat from the laser melts the material in the targeted area.
Once the laser heats the metal, the molten metal cools quickly and solidifies, forming a strong bond. The speed and precision of the laser allow for clean and narrow welds, even in very thin materials. After the weld is done, there’s often very little need for extra processing because the weld is so smooth and neat.
In some cases, a special robot arm or automated system is used to control the laser, ensuring it stays accurate and consistent throughout the welding process. This high level of control makes laser welding ideal for intricate parts and products that need precision.
Why Laser Beam Welding is the Future of Metal Joining
Laser beam welding is becoming a popular choice in many industries due to its speed, precision, and ability to create strong, clean welds. As technology continues to improve, the process is becoming even more efficient and affordable. This makes it a great solution for businesses looking to speed up production while maintaining high-quality results.
One of the main reasons laser beam welding is the future of metal joining is its versatility. It can be used on a wide variety of materials, from thin sheets to thicker metals. The laser can also weld in hard-to-reach areas, making it perfect for jobs where traditional welding methods might struggle.
Moreover, laser welding doesn’t require filler material, which can reduce costs. The precision of the laser means the weld is very clean, with minimal waste or need for post-processing. This is why many industries, from automotive to electronics, are turning to laser beam welding to stay competitive.
Top Benefits of Using Laser Beam Welding in Modern Manufacturing
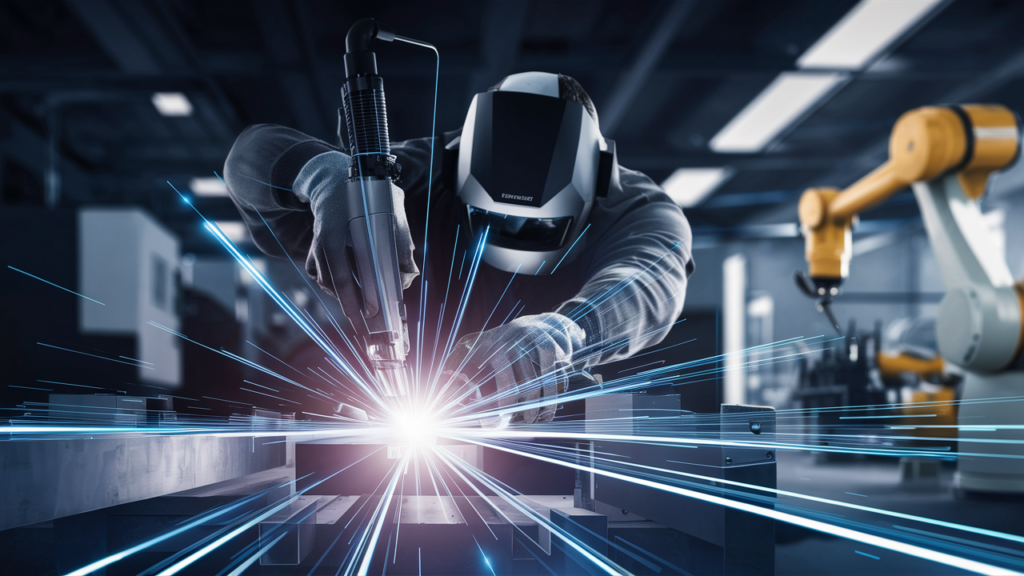
Laser beam welding offers many benefits, which is why it’s becoming so popular in industries like automotive, aerospace, and electronics. Here are some of the top reasons companies are choosing this method:
Speed and Efficiency: Laser welding is much faster than traditional methods, allowing manufacturers to produce more parts in less time.
Precision: The laser beam can be focused on a very small area, resulting in a clean and accurate weld. This is ideal for delicate parts.
No Need for Filler Material: Unlike many traditional welding methods, laser beam welding doesn’t require extra filler material, making it a more cost-effective solution.
Minimal Post-Processing: The welds created by laser welding are often so clean and neat that little to no post-processing is needed. This reduces both time and costs.
Laser welding also helps improve product quality. Since the process is controlled and precise, it results in fewer defects and less chance for errors, which is essential for creating high-quality products that meet strict industry standards.
Laser Beam Welding vs. Traditional Welding: Which One is Better?
When choosing a welding method for a project, it’s important to understand the difference between laser beam welding and traditional welding techniques. Here’s a quick comparison:
Speed: Laser beam welding is much faster than traditional methods like MIG or TIG welding. This speed can improve productivity, allowing manufacturers to produce more parts in less time.
Precision: Laser welding offers more precision than traditional welding methods, making it ideal for small, delicate parts that require exact welding.
Material Compatibility: Laser welding works well with a variety of materials, including metals that are difficult to weld with traditional methods.
Cost: While the initial setup costs for laser welding equipment can be higher, the operating costs are lower because it doesn’t require filler material and often reduces the need for post-processing.
Both methods have their advantages, but for projects that require speed, precision, and minimal waste, laser beam welding is often the better choice.
Key Industries Using Laser Beam Welding for High-Precision Results
Laser beam welding is used in several industries, thanks to its ability to provide strong, precise welds. Here are some of the industries that benefit from this technology:
Automotive: In the automotive industry, laser welding is used to create parts that need to be lightweight but strong. It’s also used for assembling components with high precision.
Aerospace: Laser welding helps create high-strength welds in the aerospace industry, where safety and precision are critical. It’s used to assemble various components of aircraft, including parts made from lightweight alloys.
Electronics: Laser welding is also used in the electronics industry to weld small parts like sensors and connectors. The precision of the laser ensures that tiny parts can be welded without damaging other components.
Medical Devices: Laser welding is used to create medical devices, such as surgical instruments, that require high-quality, clean welds.
With its ability to provide detailed and strong welds, laser beam welding is a go-to technology in many cutting-edge industries.
Choosing the Right Laser Beam Welding Equipment for Your Project
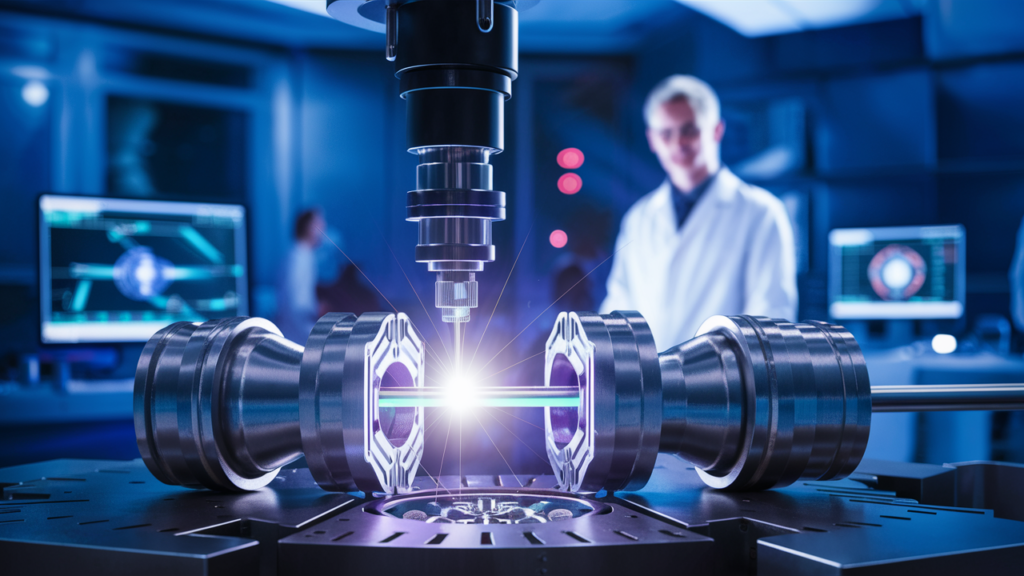
When it comes to laser beam welding, choosing the right equipment is crucial to ensure success. There are a few key factors to consider when selecting the right tools for the job:
Laser Power: The power of the laser is one of the most important factors to consider. Higher power lasers are ideal for welding thicker materials, while lower power lasers are better for thin sheets.
Type of Laser: Different types of lasers, such as CO2 and fiber lasers, offer various benefits. CO2 lasers are ideal for welding thicker materials, while fiber lasers are best for precision work.
Automation: Many laser welding systems are automated, which improves speed and consistency. If you’re working with high-volume production, choosing an automated system may be the best option.
Cost: While laser welding equipment can be expensive, it’s important to balance the cost with the benefits it brings in terms of speed, precision, and long-term cost savings.
By understanding these factors and matching the equipment to your specific needs, you can get the most out of your laser beam welding process.
Conclusion
In conclusion, laser beam welding is a cutting-edge technology that’s reshaping how we join materials. Its speed, precision, and ability to work with various materials make it a popular choice in many industries. While it might require a larger initial investment compared to traditional methods, the long-term benefits, such as faster production times and reduced costs, make it a smart choice for many businesses.
As technology continues to advance, we can expect laser beam welding to become even more efficient and accessible. If you’re looking to improve your manufacturing process, laser beam welding could be the answer. Whether you’re in automotive, aerospace, or electronics, the precision and reliability of laser welding will continue to play a major role in shaping the future of manufacturing.
FAQs
Q: What is laser beam welding used for
A: Laser beam welding is used to join metal parts with precision and speed, and it’s commonly used in industries like automotive, aerospace, and electronics.
Q: Is laser beam welding expensive
A: While the initial cost of laser welding equipment can be high, the operating costs are lower than traditional welding methods, making it cost-effective in the long run.
Q: Can laser beam welding be used on thick materials
A: Yes, laser beam welding can be used on both thin and thick materials, but higher-powered lasers are needed for thicker materials.
Q: Do I need additional filler material with laser welding
A: No, laser beam welding doesn’t require filler material, making it more efficient and cost-effective compared to other welding methods.
Q: How precise is laser beam welding
A: Laser beam welding is highly precise, making it ideal for delicate parts and projects that require accurate, clean welds.